Unfortunately, fast and tidy should not be priorities when you’re in the preparation stages before drilling or coring concrete structures. Quality and quality alone should be your number one priority, with pace and looks following secondary.
Here we will tell you why grid systems do not provide you with the quality you need to mitigate risk before penetrating a slab.
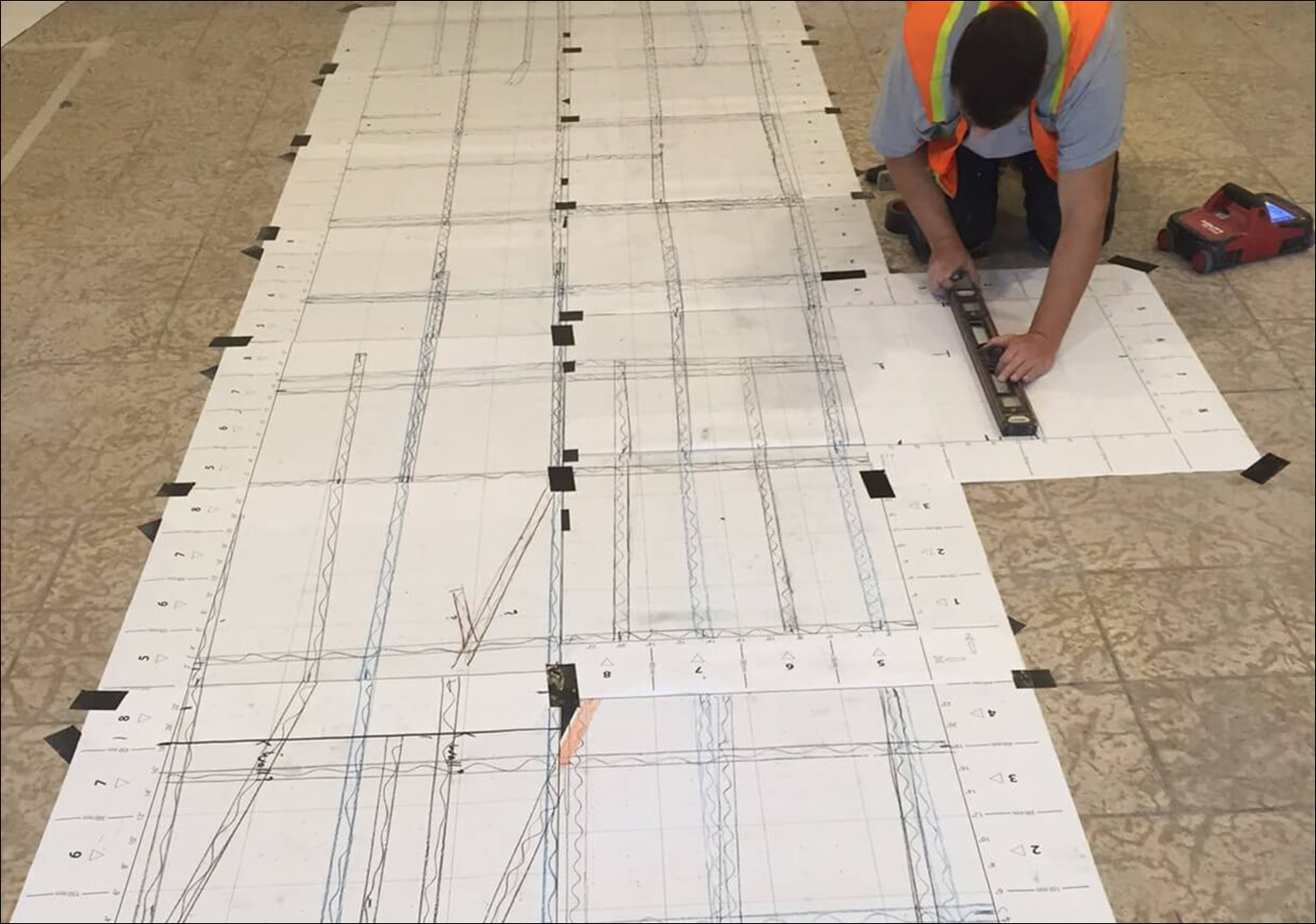
GPR is the proven technology
Concrete scanning is not a simple task, and is highly interpretive in its nature.
It requires trained technicians interpreting complex data to fully understand what lies within concrete. GPR is the proven technology that provides the most accurate information in a non-destructive way (NDT), but the methods used in different hands can generate entirely different results.
Even whilst using GPR, the grid system method of scanning an area of concrete will often lead to missing well over 50% of what actually lies beneath the surface.
Other methods are available, such as Xradar, that are confident in their results being 99%+ accurate.
.jpg)
What are paper and digital grids?
A paper or digital grid is an area of focus for a concrete scan that allows the user to clearly outline their findings against an X or Y axis. Grids range in size, but crucially are limited to the boundaries specified, and the guidelines provided by the system.
The grid method is very commonly used to report on a concrete scan, and often is used at the entry level interpretation of GPR scanning. Scanning in a grid formation is extremely easy to execute, and for this reason often comes highly recommended by manufacturers of GPR equipment. This, accompanied by relatively cheap GPR devices, creates an attractively low barrier to entry for becoming a concrete scanner.
The method requires collecting lines of data with a GPR unit in only two directions, never moving outside of the specified grid. The user makes regular passes in one direction along the equally spaced lines of the grid, before turning the device to make passes on a 90 degree angle.
When using this method, the GPR unit recommended is usually a variation on the ‘mini’ because of its relatively low cost compared to more capable equipment in the market. It tends to be an all in one, very easy to use, entry level GPR unit.
The device algorithm produces realtime data that is either transferred to a paper grid on the slab whilst scanning, or collected and transferred once complete.
The data produced is not bad, but it can only produce what it sees within the slab, along those pre-defined lines. Entry level devices themselves also tend to be anything but ‘mini’, restricting access to various tight spaces or walls with around 4.5 inches of clearance in some cases.
To accompany the markings, the GPR unit can then sometimes even produce an attractive 3D image that can be viewed by the client to help inform their next move, which typically is to cut or core into the concrete.
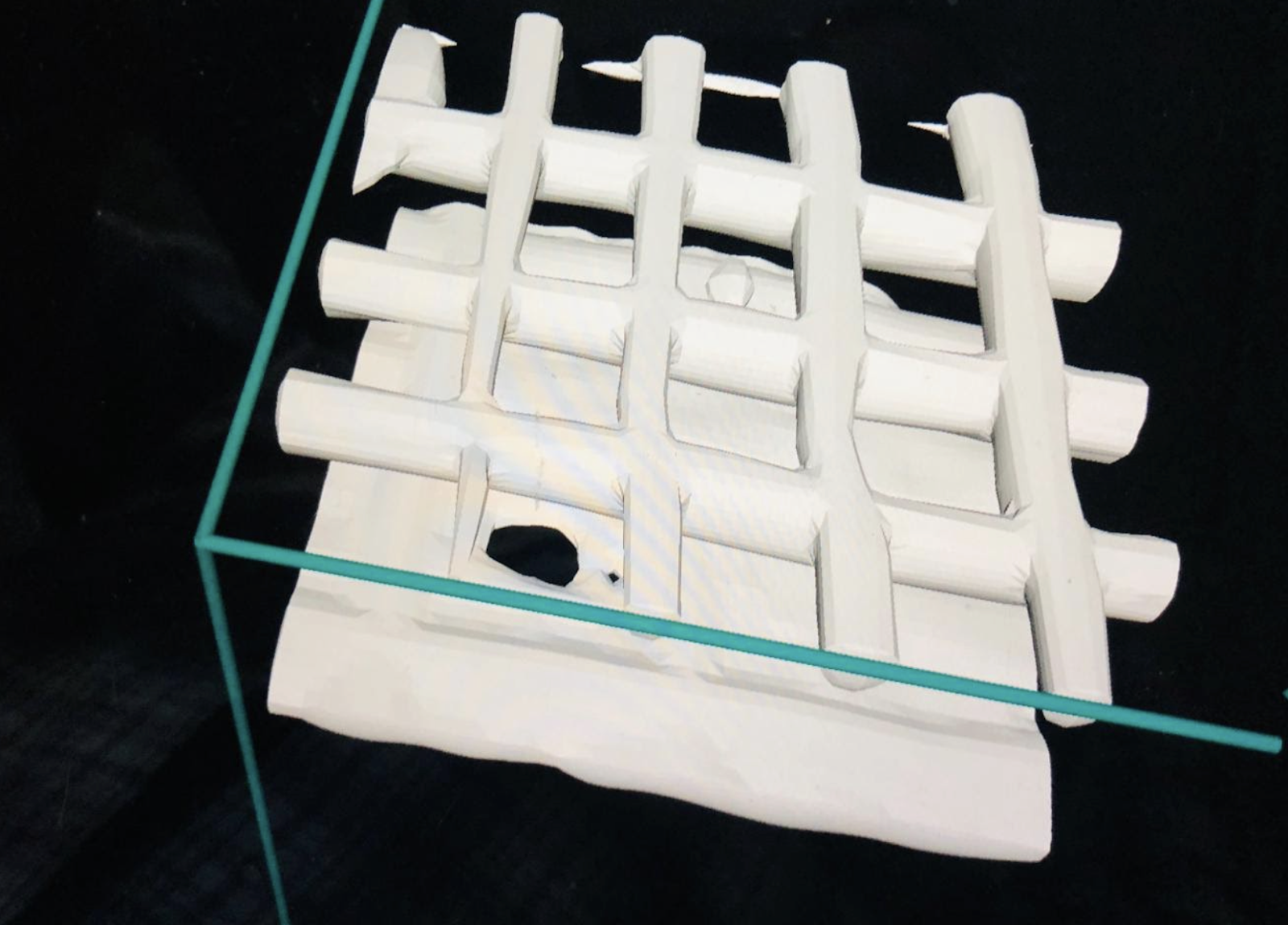
Why are paper grids not an accurate method of collecting data?
Before outlining the limitations of collecting data with grids, we need to understand the capabilities of radar.
Radar does not travel through metal, it gets reflected back to the receiver, which is exactly the reason it is useful. If faced with very dense rebar or mesh, you will find that most of the radar is reflected back, and there is very little data available showing what’s underneath. This is why interpretation of data and understanding of true deliverables are key whilst concrete scanning. If a method relies solely on software to interpret the subsurface, then mistakes will be made.
The computer algorithm that creates the above paper grid image works on GPR amplitudes, so the top rebars have the highest amplitudes and thus are the clearest in the image. Conduits and lower rebars have lower amplitudes, and will therefore often not show up on the image without further investigation. Two of the most common scenarios where these targets won't show are:
- That they're within the Fresnel zone with another more significant target
- That they are directly below another target and their amplitude is "shadowed"
Not being able to see targets within the concrete slab will regularly cause massive issues, and the risk of hitting one of these targets whilst cutting or coring increases.
However, what does show usually looks clear and tidy. In some cases you are even able to view the results in augmented reality, which looks good, but doesn’t necessarily mean that what you’re seeing is actually every target embedded within the concrete.
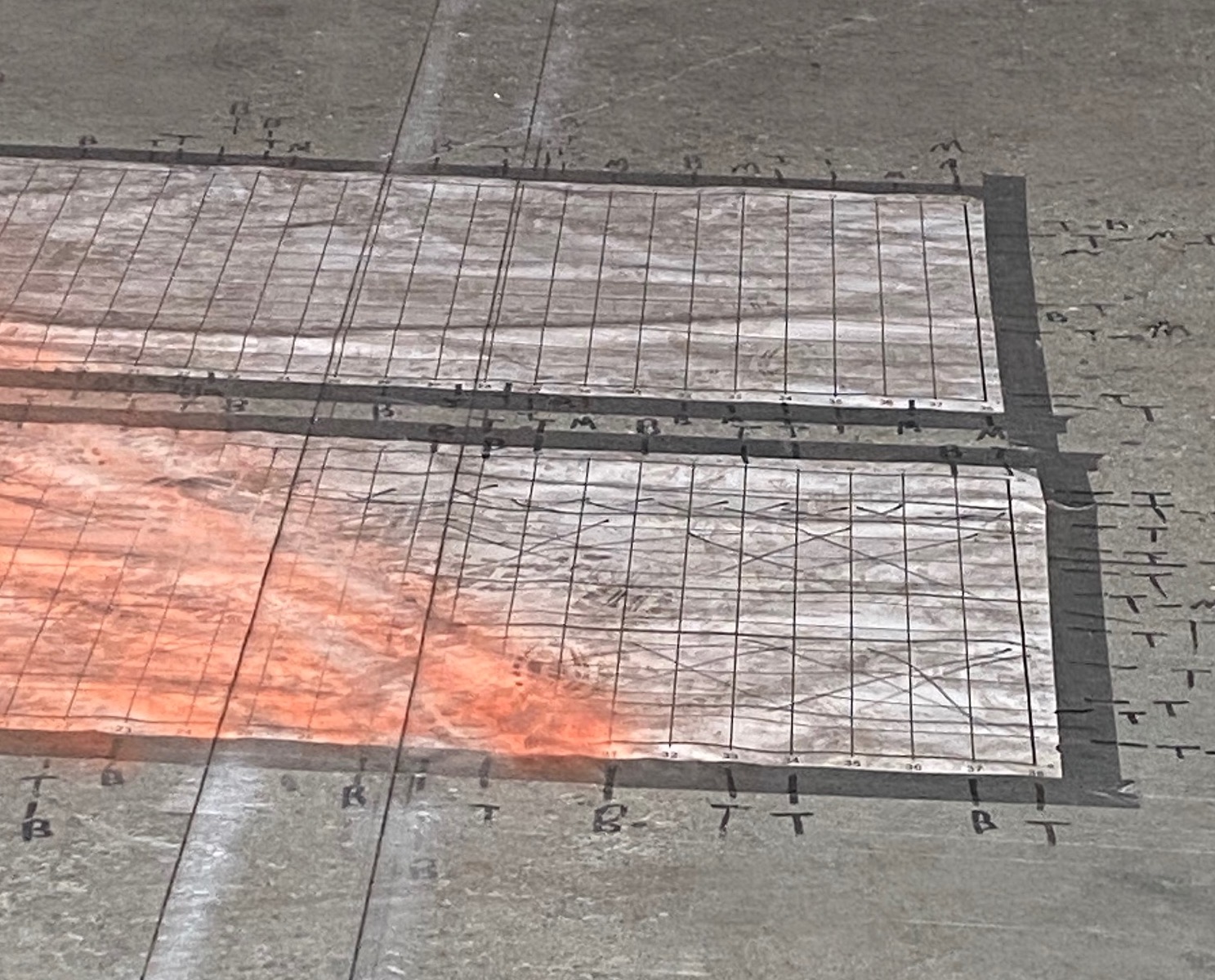
The use of a grid limits you in understanding the true patterns of the subsurface targets, and simplifies the method of scanning to such an extent that it becomes extremely misleading. When things become misleading and targets are hit, the user will typically blame the limitations of GPR, eroding its name. In reality, the limitation does not lie with the technology, but the ability to interpret the data correctly.
A further limitation to the grid scan is in the transferral of data. Targets are displayed digitally on a screen and need to be transferred to the slab after the grid scan is completed. With the user often marking the targets on the grid paper after the grid scan is completed, there’s risk of inaccuracies, which increases the risk of accidental damage to embedded targets. Furthermore, the markings on paper are not very durable (as highlighted in the picture above), and should the tape holding the grid paper to the slab ever come loose then the whole scan will be unusable. In this case the accurate location of the targets is impossible to be verified without a repeat scan.
So what can be done to use GPR to its full potential, increase the accuracy of the results, and reduce the risk of hitting targets?
Reliable methods and true deliverables
When reviewing the methods of scanning concrete for hidden objects, you have to question what the true deliverables are for the wider project. Are you being asked to scan a 3x3 proposed core location, or are you being asked to find a location that not only works within the parameters of the project, but reduces risk to almost nothing.
Without the limitations of a grid and it's method, you can freehand scan around the area and are not fixed to that location.
Scanning around the area, as well as into awkward places (such as against a wall), gives you a wealth of information to better interpret the target placements. In a scenario where your grid happens to have been placed over thick rebar, you would simply miss what’s underneath, and the consequences could be dire.
Flexibility and understanding is key.
In addition to this, methods such as Xradar enable you to understand the layout of the subsurface before you will have even had an opportunity to stick down some paper.
With the flexibility to take data from multiple passes, in multiple locations, at multiple angles and multiple frequencies, an Xradar technician is able to fully understand the slab in order to make informed recommendations on the most complex of scans.
.jpg)
Xradar case study: Rescanning a grid
Xradar quite regularly are asked to more thoroughly scan an area, which might have been scanned by a competitor. This following case study is quite typical of the findings.
Figure 1 below shows the findings of a 3D grid scan whilst scanning simply the grid lines shown. This shows quite clearly the top rebar, which will have been marked on the grid as a target to avoid.
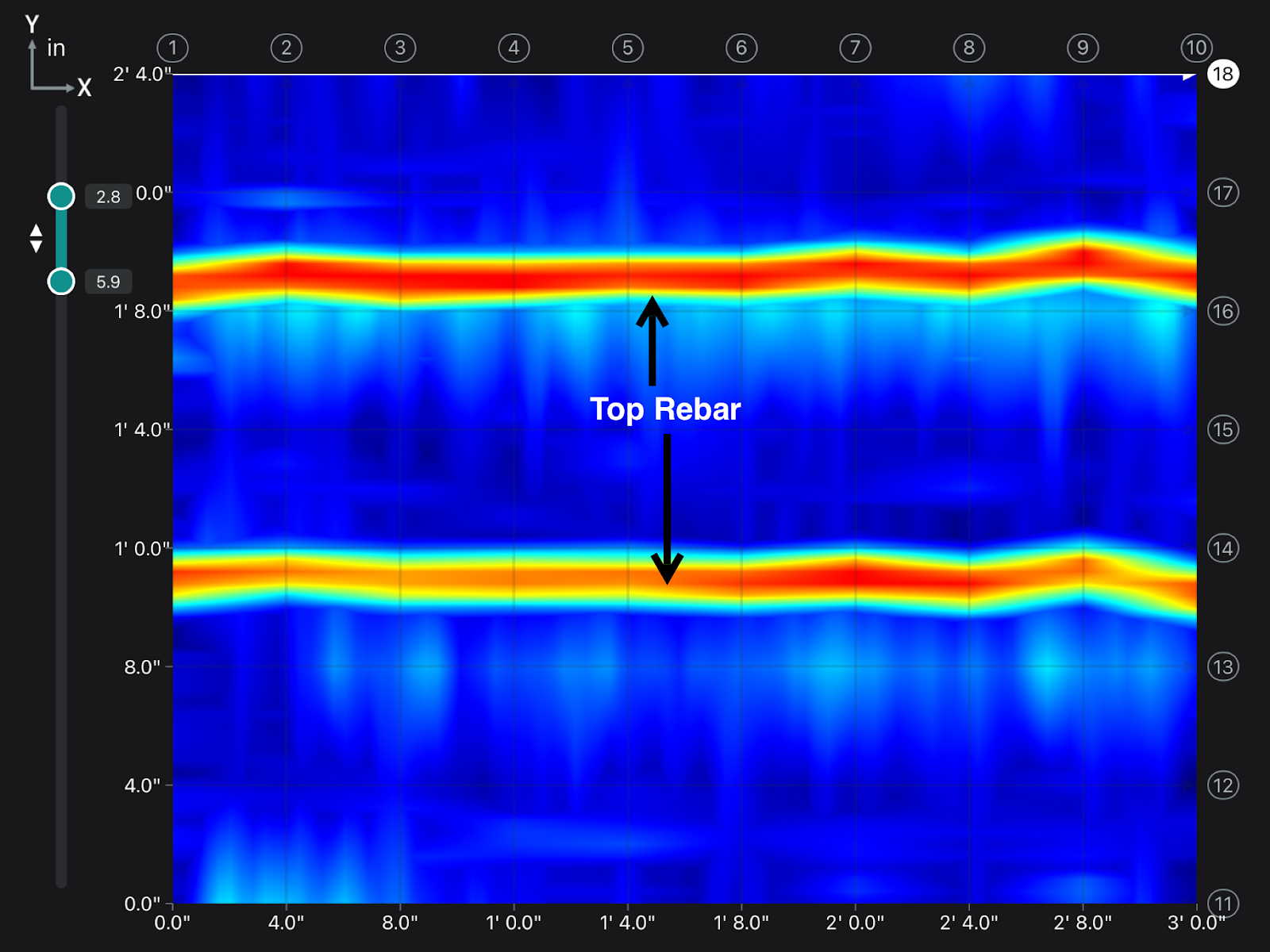
Figure 2 and 3 shows the findings when using more advanced methods, which show vertical bottom bars and missing conduits.
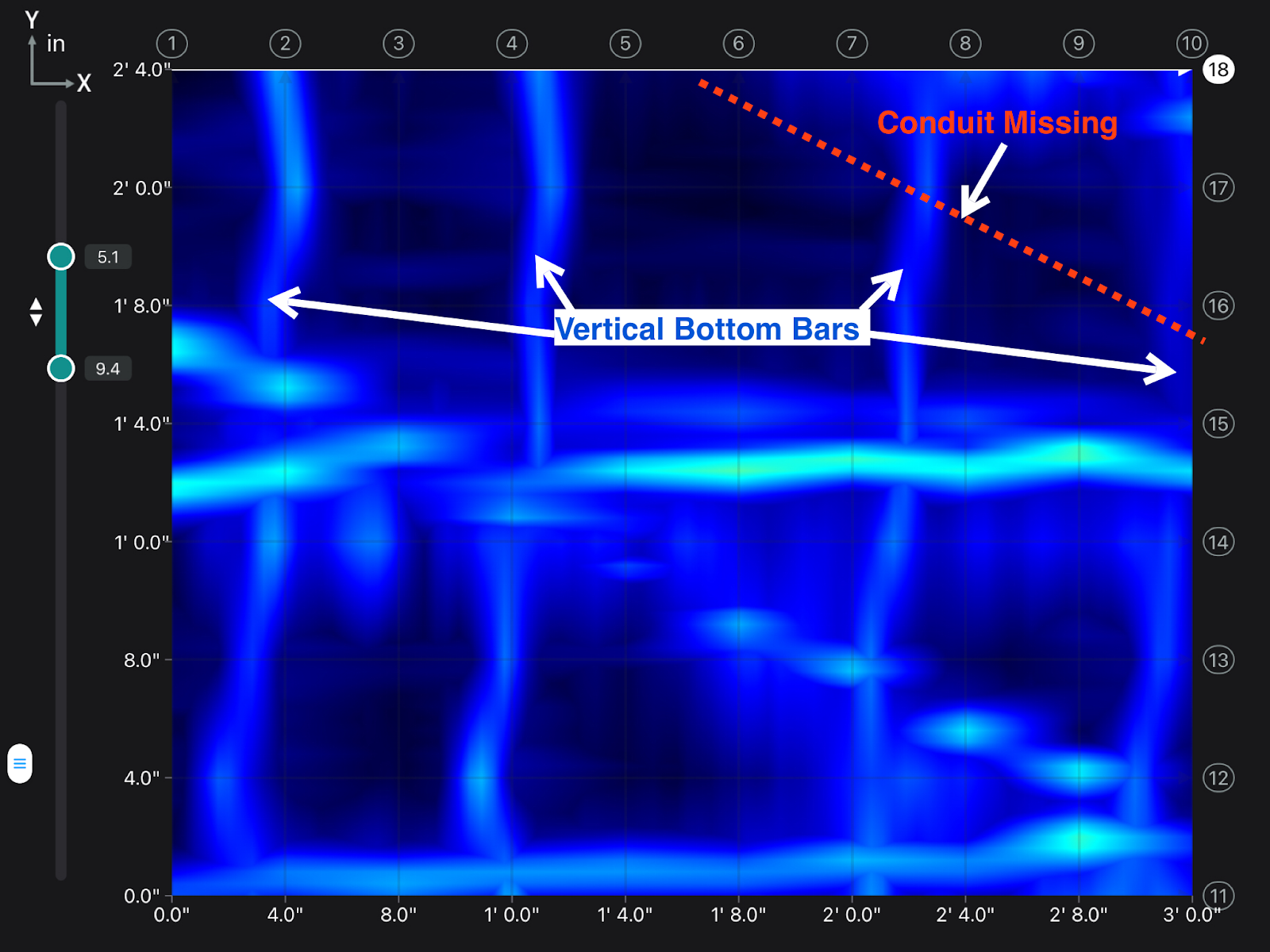
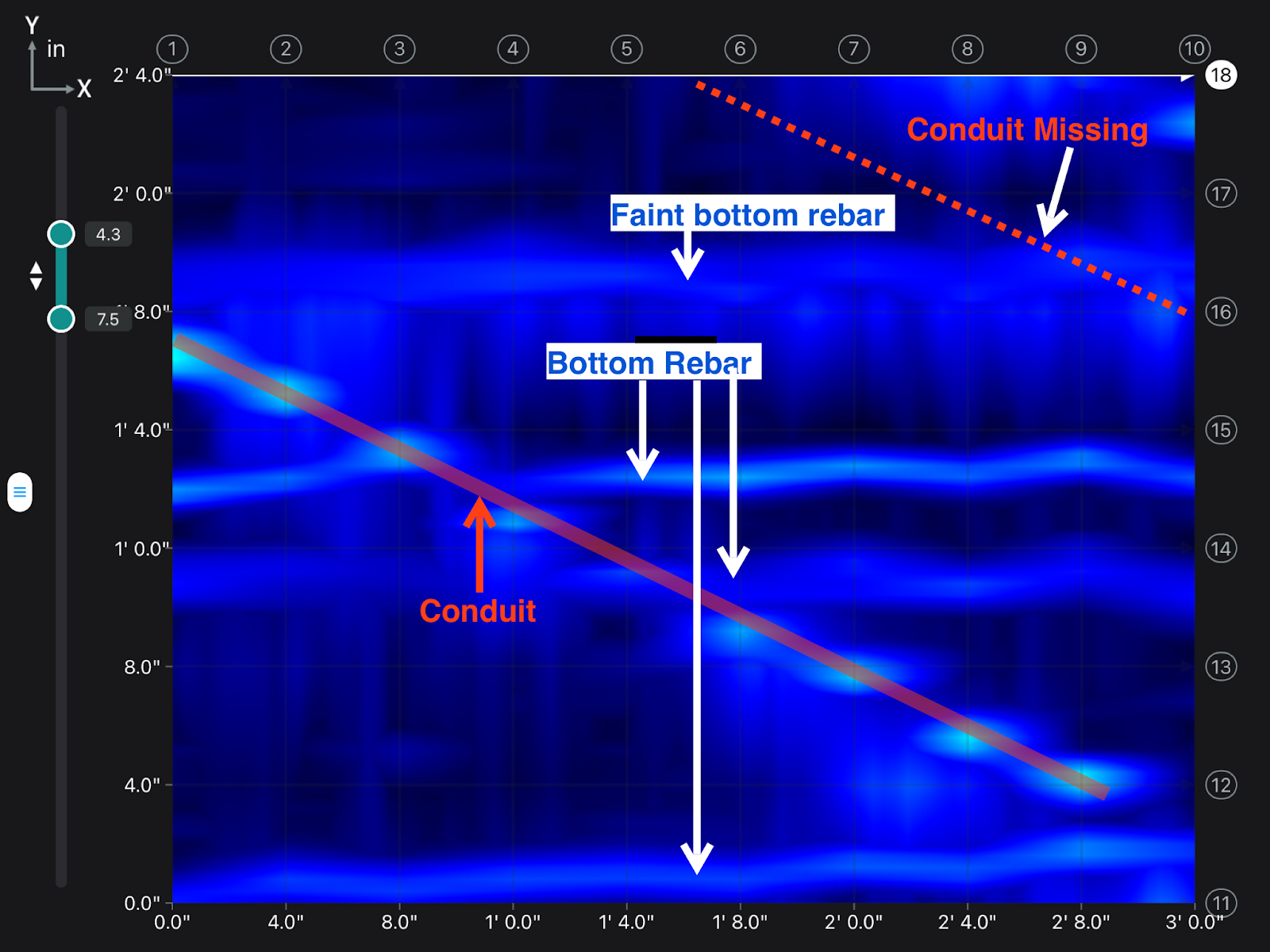
Then finally, figure 4 & 5 shows the final scan drawings, and further verifies the interpretation of the data. The target patterns are also shown logically on a large area, fully understanding the contents of the slab.
.jpg)
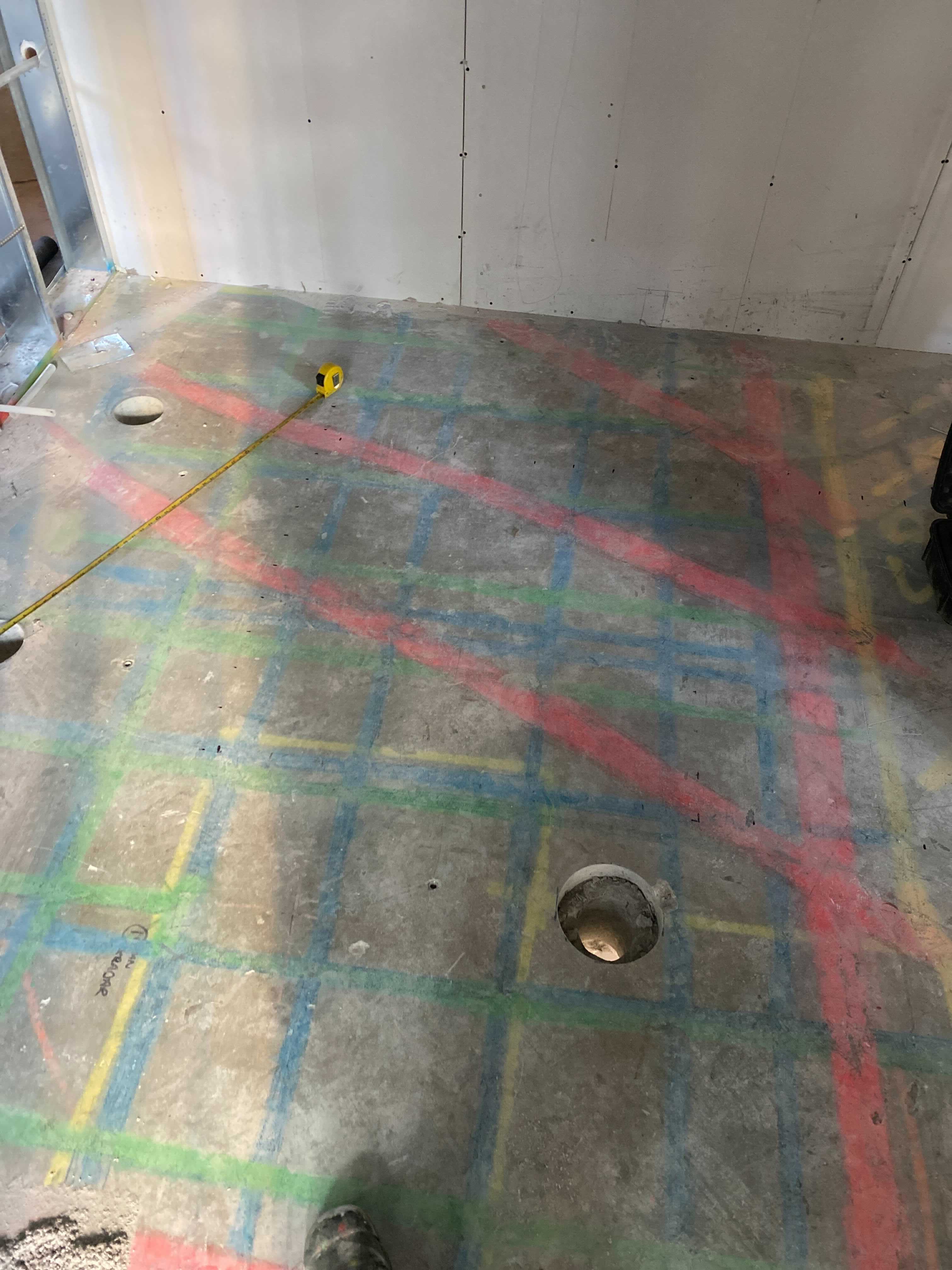
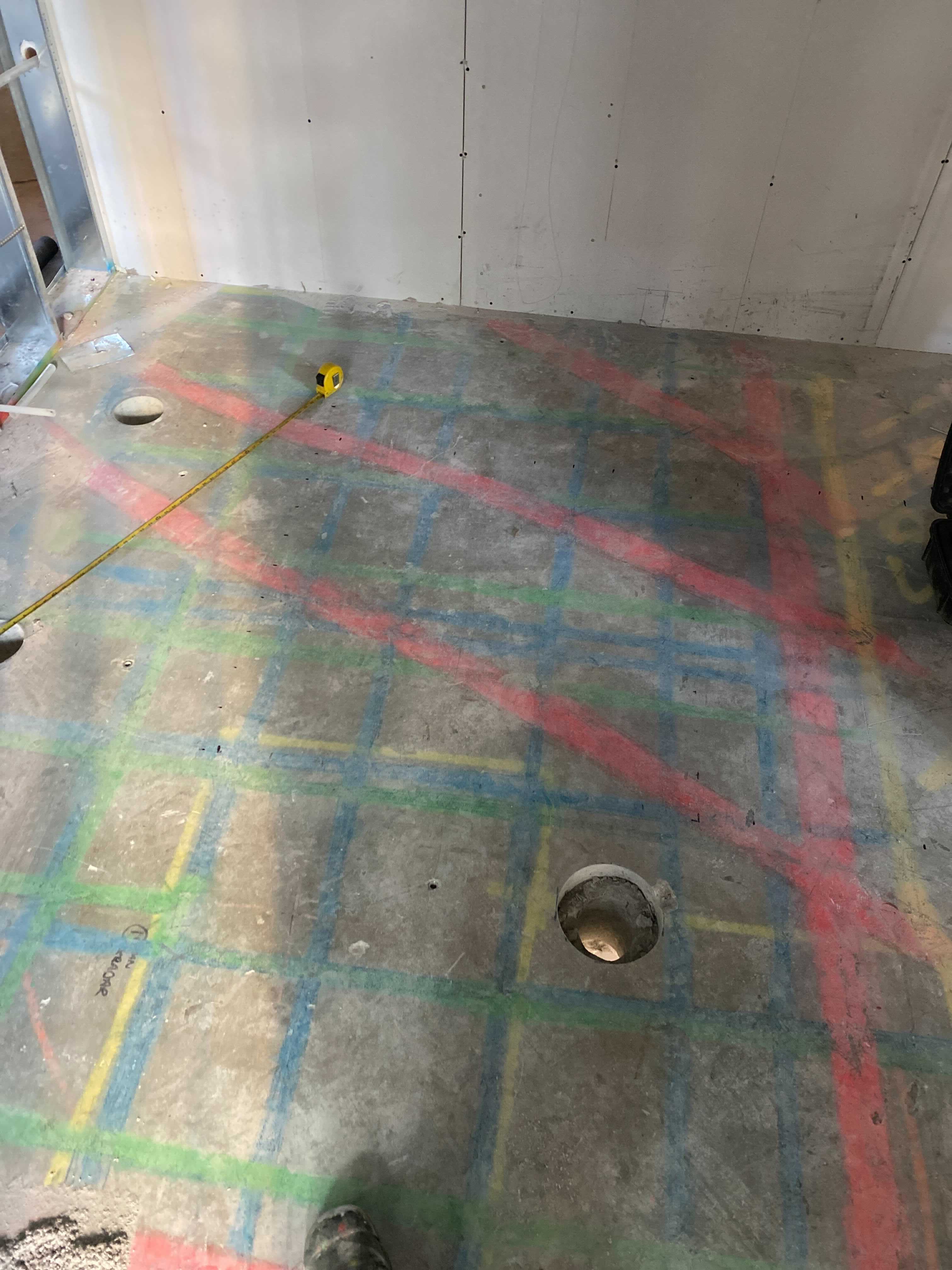
What is next for GPR in the scanning industry?
From a manufacturers standpoint, GPR equipment is selling fast. If you choose the correct model for your purposes then you are able to start scanning concrete with very little training.
In the short term manufacturers are happy, because units are selling quickly. The concern is that in the long run poor operation may give the excellent technology a bad name, causing customers to avoid companies that successfully use those methods.
Significantly, there are very few regulations around concrete scanning. If at any point the construction industry demands tighter regulations on scanning methods, then GPR use will be the safest, fastest and most cost effective way to meet these.
Conclusion
Scanning concrete with complete accuracy demands an expert level of interpretation.
The use of entry level devices and grid methods is becoming widely available at a relatively low cost. The issue found with the low cost is that it often sacrifices quality, and therefore safety. That low cost then becomes a very high cost, once a mistake has been made.
The temptation to use grids is clear to see; it’s cheap, it’s tidy, it makes the process look simple. In reality, its guess work and lack of understanding causes far more problems than its worth. Understanding the deliverable of a concrete scan is key to that scan’s success, and if correctly understood, it’d lead to using a more thorough method of data collection.
GPR as a technology is exceptional in well trained hands, but its reputation will remain in the balance until proper regulations are in place.
If you’d like to learn more about Xradar head to our blog pages. To speak to one of our technicians about your next project please get in touch.